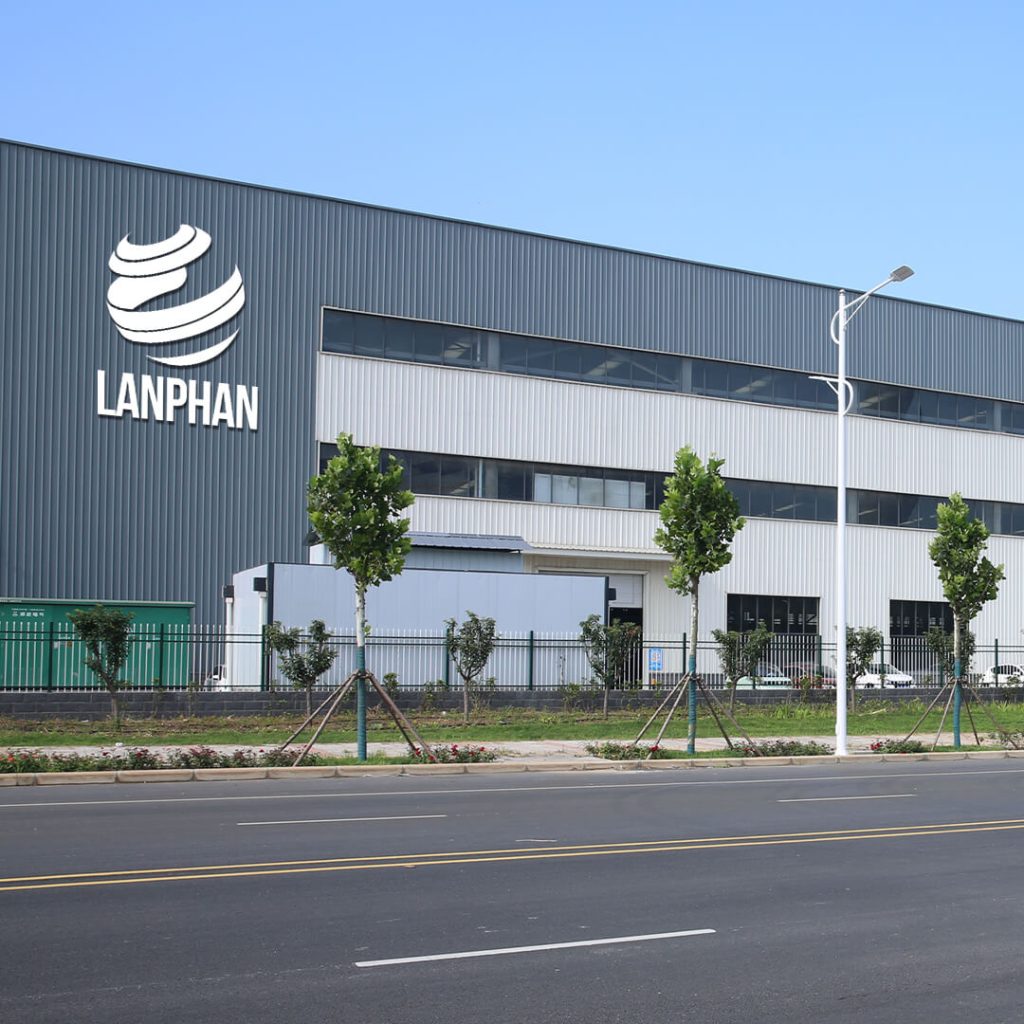
Overseas warehouses: United States, Australia, Thailand
We have many overseas warehouses
What We Do.
Botanical Extraction
Plant extraction involves obtaining beneficial compounds from plants for various applications, harnessing their natural properties for health, beauty, and other purposes.
Freeze Dryer
freeze dryer removes moisture from food, preserving its quality and extending shelf life. It’s used widely in homes, labs, and commercial settings to produce long-lasting, high-quality food.
Pharmacology
our company builds a strong technical team to support the production and manufacturing of pharmaceutical machinery, meeting customer needs and maintaining a leading position in the industry.
We Provide Professional Services.
Customized Services for Clients:
- 20+ Years of Experience
- Tailored solutions for specific requirements
- Customer needs assessment and analysis
- Customized services for particular industries
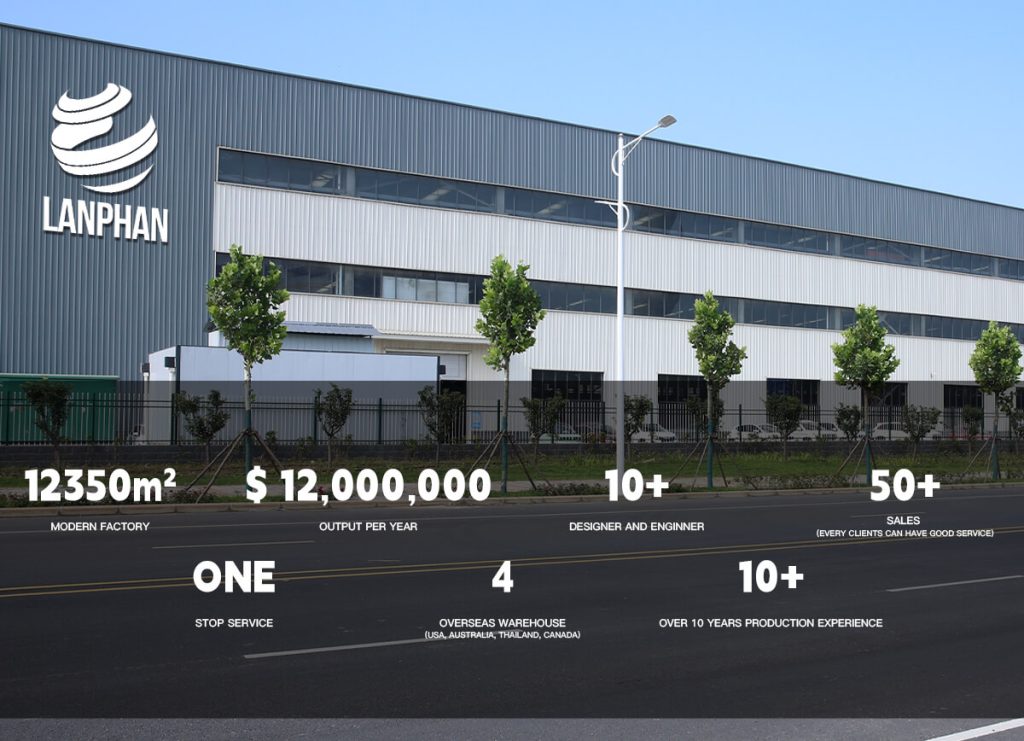
We are a professional and reputable company.
Christine Yap
Machine was shipped in a very secured packaging. It is my first time to operate this kind of machine so I had to learn for a while. But Mr. Tom, their agent has been very helpful and responsive to my inquiries. I would highly recommend purchasing from their company.
Kevin Dean
I love saving my food and having the nutrition there. I know what’s in it and I know where it is when I need it. I don’t have to worry about it needing used in 18 months either. The main company has always stood by their product and my one teeny issue was remedied the same day. Always prompt in their emails and replies. Greatly appreciated 🙂
John Quqa
I love my freeze dryer. With special dietary restrictions it is hard to purchase food storage. Now we can make our own and know we can have good food we can actually eat. Also a great way to preserve leftovers. Fantastic for fresh produce from the garden. I even purchase bulk food to save money and then freeze dry it.