What is the purpose of a spray dryer?
A spray dryer is a device used to transform liquids or slurries into a dry powder form. It works by atomizing the liquid substance into tiny droplets and then rapidly drying these droplets using hot air or gas to remove moisture or solvents. This process enables the production of fine powder or granules with specific particle size, shape, and density, facilitating storage, transportation, or further processing. In the food industry, spray dryers are employed to produce products like milk powder, coffee, and powdered flavors. In pharmaceuticals, they are used to create dry forms of medications for easier dosing and preservation.
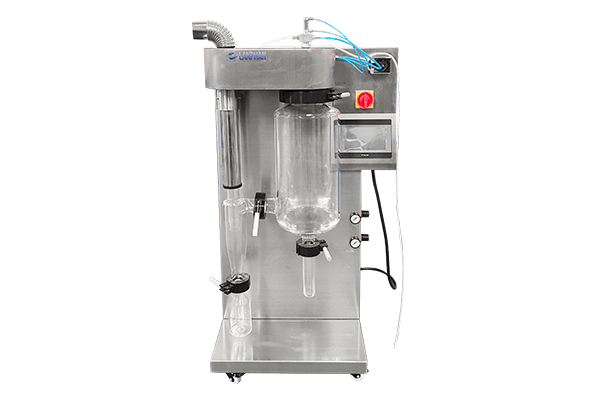
2L Glass Spray Dryer
- Evaporated water : 1500ml/h~2000ml/h
- The largest feed rate : 2000ml/h
- Electric heater : 3.5KW AC220V
- Maximum quantity of wind : 5.6 m3/min
- Maximum air pressure : 1020 Pa
- Nozzle diameter : 1.00 mm /0.04inch(optional)
- Package dimension (L*W*H) : 600*700*1200(mm)/23.62*27.56*47.24(inch)
- Weight : 125KG/130KG(275.58lbs/286.60lbs)
2L Stainless Steel Spray Dryer
- Evaporated water : 1500ml/h~2000ml/h
- The largest feed rate : 2000ml/h
- Electric heater : 3.5KW AC220V
- Maximum quantity of wind : 5.6 m3/min
- Maximum air pressure : 1020 Pa
- Nozzle diameter : 1.00 mm /0.04inch(optional)
- Package dimension (L*W*H) : 600*700*1200(mm)/23.62*27.56*47.24(inch)
- Weight : 125KG/130KG(275.58lbs/286.60lbs)
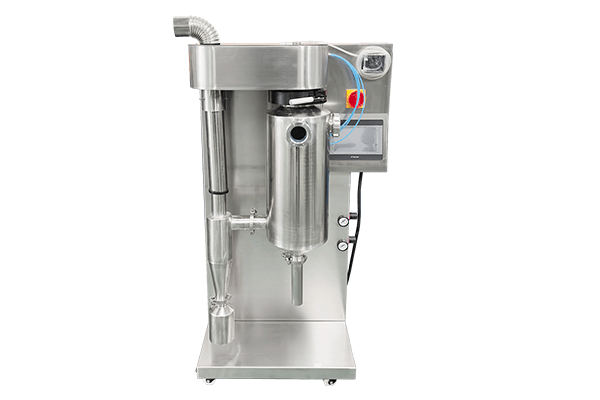
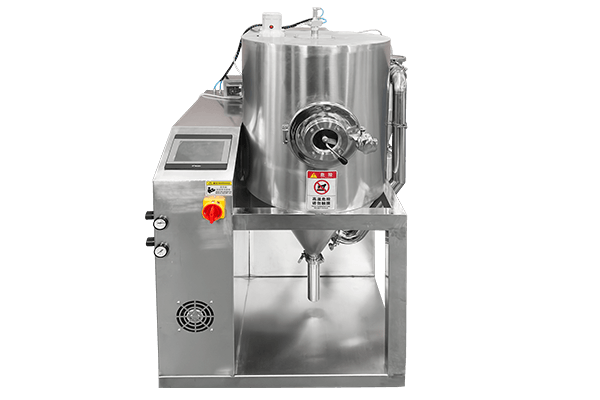
3L Two fluid spray dryer
- Evaporated water : 3000ml/h
- The largest feed rate : 3000ml/h(adjustable)
- Nozzle diameter : 1.00mm/0.04inch (optional)
- Dryer time : 1.0 ~ 1.5 S
- Draught fan : 0.55KW 100m³/h
- Package dimension (L*W*H) : 800*800*1450(mm)/31.50*31.50*57.09(inch)
- Package Weight : 148KG/326.28lbs
3L Centrifugal spray dryer
- Evaporated water : 1500ml/h~3000ml/h
- The largest feed rate : 3000ml/h(adjustable)
- Nozzle speed : 36000r/min(adjustable)
- Dryer time : 1.0 ~ 1.5 S
- Draught fan : 0.75KW 140m3/h
- Package dimension (L*W*H) : 1100*900*1600(mm) / 43.31*35.43*62.99(inch)
- Package Weight : 150KG/330.69lbs
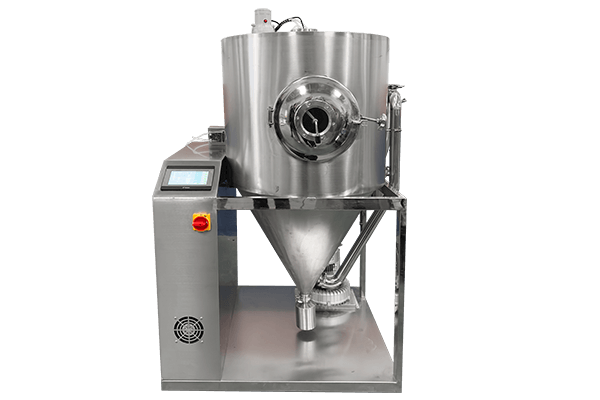
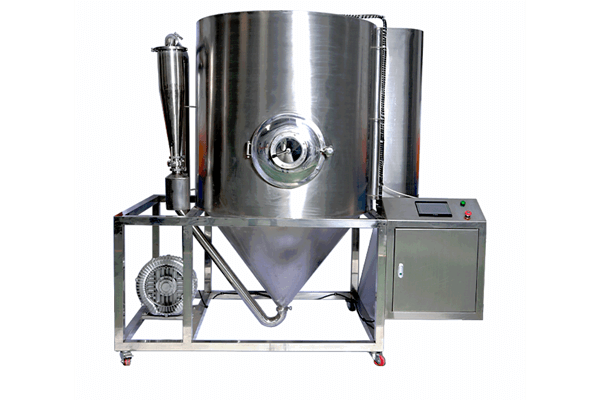
LPSD-5 Spray dryer
- Minimum feed amount:50mL/h
- Average drying time:1.0~1.5S
- Electric heater power:9KW
- Draught fan:3KW Maximum wind velocity 360m3/h
- Machine power:13KW 380V
- Machine Dimensions:2000mm(height)×1600mm(length)×1200mm(width)
Get a quote now!
Why Is Spray Drying Better?
Efficient Drying
Unique spray technology rapidly atomizes the liquid, facilitating swift interaction with hot air and achieving high-efficiency drying to enhance production efficiency.
Customized Particle Size
Precise control of the final powder’s particle size is achievable by adjusting operational parameters, meeting specific requirements for particle size in different products
Product Quality Assurance
The rapid execution during the drying process reduces exposure time for heat-sensitive substances, aiding in maintaining product quality and the integrity of active ingredients.
Wide Applicability
Widely used in industries such as food, pharmaceuticals, and chemicals, it can process various liquid raw materials, including milk and medicinal liquids.
Energy Efficiency And Environmental Friendliness
Incorporating advanced energy recovery techniques minimizes energy waste, aligning with environmental conservation requirements.
User-Friendly Operation
The equipment features an intuitive control interface, facilitating easy operation and monitoring, thereby reducing operational complexity.
Lanphan Spray Dryers: Precision Engineering for Customized Powder Solutions in Chemical & Food Industries
lanphan has spray dryers that are built on over decades of experience and 180 references from around the world in the chemical and food industries. The unique know-how that goes into the design of atomizers offers high reliability and a sophisticated approach to provide the right particle characteristics that are suitable for the application you want. From pilot facilities and industrial equipment: lanphan provides a full variety of spray drying units as well as services.
Principle of Operation
The lanphan dryers have been made for use to dry liquids and make them into powder through an atomizer within a high-efficiency range. This delicate drying is mostly utilized to dry heat-sensitive products.
The atomizer breaks the liquid into tiny droplets, then sprays it into the hot stream of air in which the bulk of the liquid evaporates within just a few seconds. After that, the dried powder is isolated from the surrounding air using either a cyclone or the filter system. The dryer downstream can be outfitted with coolers, fluid beds and agglomerators, which further dry the powder prior packaging unit.
Characteristics
Lanphan Spray dryers were made to meet the unique demands of our clients and provide a large degree of flexibility in design.
Atomization can be achieved through the use of centrifugal wheels, rotating atomizers, high pressure sprayers and dual-fluid sprayers. This range of technologies allows for the particular particle size requirements to be met in each application.
Heating systems that are indirect or direct can be offered in accordance with the industry standards applicable to the particular product. The temperatures of the intake can vary between 100degC for extremely temperature sensitive items to 750degC for some inert chemical products.
Self-intense and closed circuit dryers are available to permit organic solvents to be dried, and to comply with environmental requirements.
A variety of chamber sizes are employed together with a variety of residence times to give the required particles’ size as well as the moisture level of the powder that is produced.
Agglomerated items are created through the integrated fluid bed, fines recycle systems and external fluid beds. These powders are used extensively within the food industry.
Special Features
- Internal fluid bed
- External fluid bed
- Brooms for air
- CIP stands for Cleaning In Place (CIP)
- Agglomeration of fluid bed
- Product cooling systems
- Automated control system
- ATEX requirements
Advantages
- Shape, size, and shape of the controlled particle and density
- Atomizers for nozzles and Rotary
- The solution is customized for every product
- Retention time that is tuned
- Systems integrated
- Many different designs
Fields of Application
Spray dryers are utilized to dry various items, particularly when there are strict hygienic requirements for the point of finalization (as within the industry of food) or if specific particle properties are required to meet. Because it is a delicate drying method as well, it is utilized for drying heat-sensitive products.
Lanphan Spray Dryers are employed for a variety of purposes. To ensure optimal operation performance, every lanphan dryer is custom-designed. The whole equipment (e.g. an atomization device) is meticulously selected and adjusted to achieve the best. With an internal fluid bed as well as external fluid bed rotary atomizers, high-pressure nozzles, twin-fluid nozzles as well as homogenizers, the spray drying system can be adjusted to meet the customers’ requirements.
The lanphan’s team of experienced spray drying experts are always determined to find the best solution for your specific needs for each customer, such as e.g. dust-free powder and aggregated powder etc.
With our vast experience and expertise in the field of particle engineering Our clients always get particles with the ideal shape size, density and shape.
Based on the requirements, it could be helpful to conduct CFD flow simulations first or run testing for drying with our fully-equipped pilot plant located in Germany.